Trending now

New Accessories
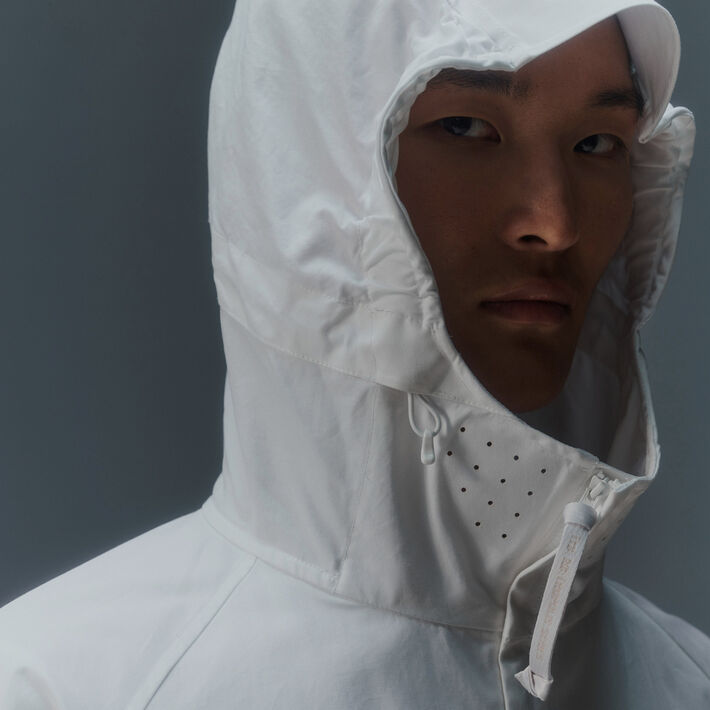
Metropolis Series
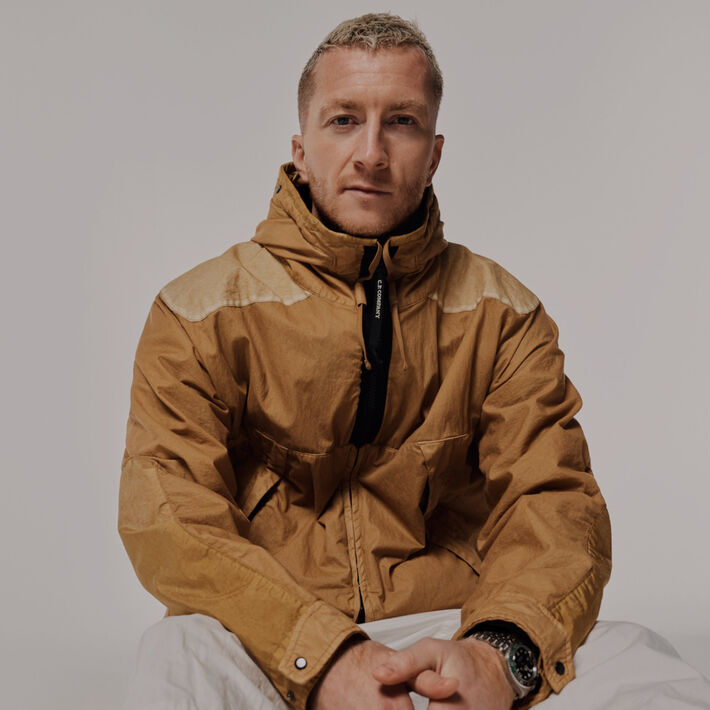
SS024 ADV Campaign
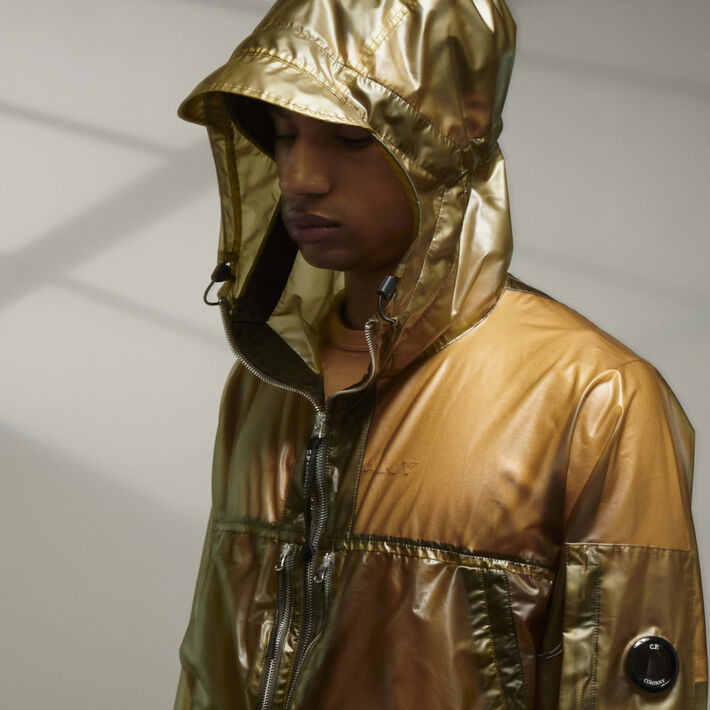
PiUM + 50 Fili Gum Mixed
about
C.P. Company
In 1971 Massimo Osti, the revolutionary designer internationally recognized as the “godfather of sportswear”, founded Chester Perry brand, renamed into C.P. Company in 1978.
The brand immediately found favour thanks to its subtly non-conformist interpretation of functional men’s wardrobe classics.
For more than 45 years the brand has continued to pioneer it’s signature hybridization of archival military, work and sportswear models, combining them with intensely researched, cutting-edge, Italian fabric innovation.
This fabric innovation has also been heightened by the use of garment dyeing, a technique C.P. Company was the first in the world to develop in the mid 1970s, in which fully-finished garments made from multiple fabric and fiber are dyed as final step, producing clothing with unique chromatic richness and tone-on-tone subtlety.
C.P. Company is easy-to-wear, feeling like you’ve always owned from the moment you first try it on, but at the same time distinctively in its details, combining tradition, innovation and performance.